Hard Rock Band
- Market Coordinator
- Mar 21, 2019
- 4 min read
While I've come a long way since my early days at Summit Sales & Equipment when I thought packing was basically bubble wrap for pumps (not a joke), there are still times when I feel like an idiot around here. One of those times was yesterday, when this exchange took place:
"Hey Kyle, we're going to want to get some video of the hardbander."
"Okay, cool. Wait, what's a hardbander?"
Thus, another adventure begins. Let's find out a) what a hardbander is and b) why it's cool that we now have one.
First stop: the fab shop, since I had heard this thing was located there. I was also told that it was not yet ready for the internet, but I'm breaking rules today. If you know anything at all about Summit Sales & Equipment, know that I'm not afraid of a "before" picture, because we have the best machinists, welders, engineers, and fabricators in the world working for us. We'll get the thing looking perfect and working even better.
So here's a hardbander.
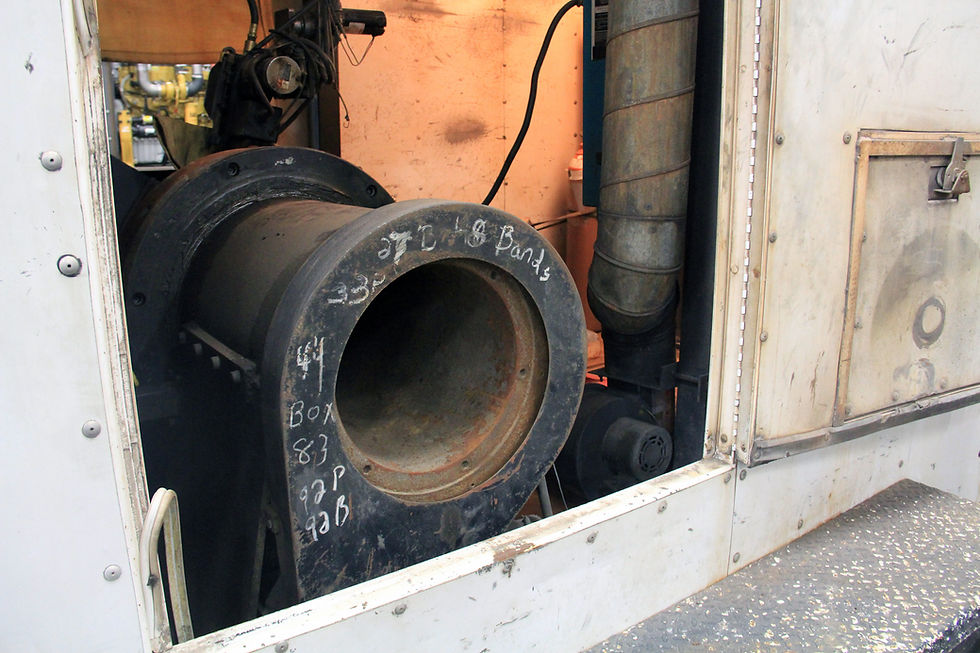
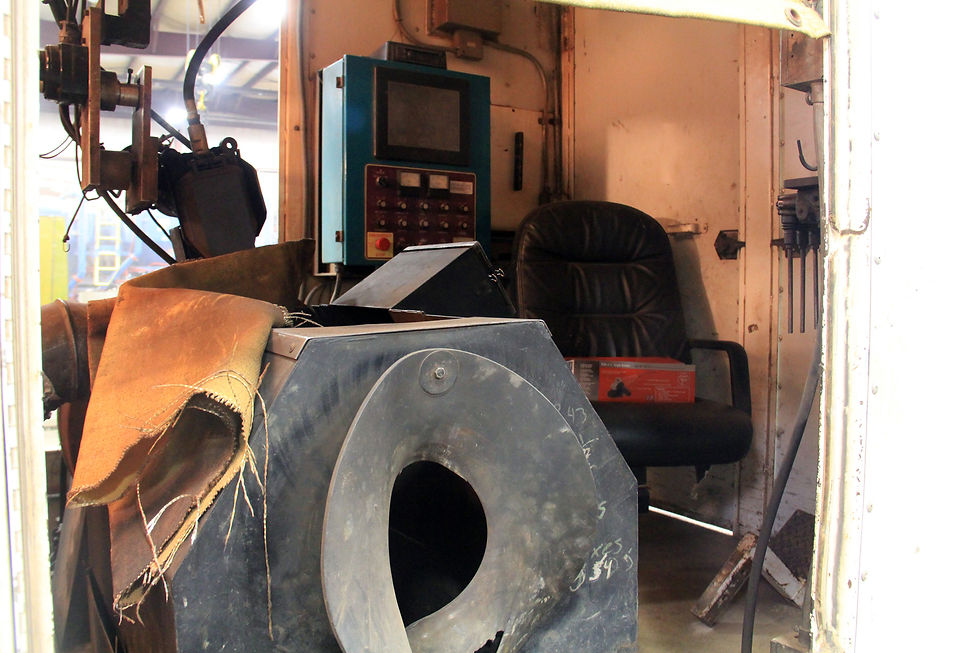
Doesn't seem like an altogether terrible situation back there, it's not too often you get a decent place to sit while working with equipment like this. Throw a cup holder in there, and it would be perfect.
There's one other place I like to start when I'm starting from zero, and that's the Schlumberger Oilfield Glossary. I have no idea why Schlumberger decided to publish a glossary of oil and gas terms (I suppose it qualifies as something we marketing types call top-of-the-funnel content), but I certainly appreciate it.
Anyway, here's what it says about hardbanding:
A process in which a wear-resistant alloy is applied to the tool joints of drillpipe or drill collars to prolong the life of oilfield tubulars. Hardbanding is applied where rotational and axial friction associated with drilling and tripping create excessive abrasive wear between drillstring and casing, or between drillstring and rock. Hard alloy overlays are applied to the points of greatest contact, typically using advanced welding techniques.
Makes sense. After all, you have stuff spinning with a lot of force as it drills through the casing and then the earth's crust (and then is tripped in and out as part of the whole process), some friction is bound to happen, especially since the tool joint is a bit wider, and it's bound to be pretty damaging when it happens. Have you ever seen the demo where they drop a car off of a building and tell you to not drink and drive at prom or whatever? This kind of reminds me of that, because the damage at 40 mph is exponential, not linear, compared to the damage at 10 mph. Welding some stuff on top of the pipe seems like a pretty decent idea with that in mind.
So let's do a little more digging on this.
Back in the olden days, up until the 1990s, tungsten-carbide particles were attached to the pipe, which did a fantastic job protecting the pipe itself, but a terrible job on the whole "don't cut the casing around the pipe and cause failures" thing. So, as we tend to do quite frequently in this industry, we came up with a new technology, hardbanding, which is flatter and more friendly to the casing while also carrying out the needed protection duties to the most sensitive areas of the pipe.
Furthermore, hardbanding can be done with different alloys, optimized for the type of earth you're drilling, the chemicals being used, and any other variable that might come up. Extremely awesome. I love learning about things that smart people have chosen to do with their lives.
Here's a nice look at the whole process.
Or, if you're not a video-type person, here's the bottom line, some hardbanding at the tool joint, the place on the pipe opposite the business end where it's most typically applied. Which makes sense, after all, the whole "joint" part of that phrase comes into place because you're talking about a piece that's fabricated separately, then welded on later - so it's a point of vulnerability.

The thing that's really pretty great, if you're us or one of our customers anyway, is that we also do drillpipe inspection and testing out of our West Virginia facility - in fact, we recently upgraded our system, which is great for customers in a bunch of ways (that I blogged about a while ago). As slick as hardbanding is, it does wear down eventually, just like most things in life, and needs to be reapplied several times over the life of the pipe and the drill string. That reapplication can occur in the field and - would you look at that?! - our hardbander happens to be in a trailer.

Basically, we're your people for pretty much anything that involves keeping your drill humming efficiently. And I haven't even mentioned our part sales yet, should you be in need of any other downhole fun.
So give us a call, eh? Whether it's this, or pretty much anything else, we can probably help you.
Happy drilling,

Comments